Case History – RHOSS
Made in Rilheva – A real Internet of Things story
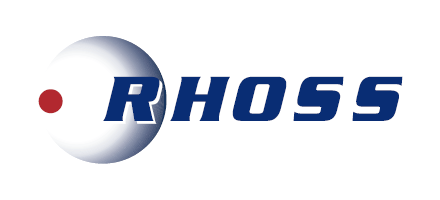
Goals and challenges
Rhoss installed first TurboPower units – our newly designed machinery with Turbocor compressors – on the roof of an important building in London, at Sloane Square, few steps away from Westminster and Buckingham Palace.
A primary requirement was to actively monitor the machines behaviour both during startupand in the long run.
We could also modify unit parameters directly from Rhoss HQ in Italy, tuning the thermal charge and avoiding unsuitable working conditions. As we couldn’t access the building internet network, we leveraged the Rilheva gateway embedded 3G connection to connect to the machinery PLC via 3G network.
Rilheva solves
Rilheva IIoT Platform’s VPN CONNECT service, combined with the 3G network connection, was essential for connecting to our machines and manage them as if they were physically located in our HQ in Italy. This allowed our Service team to remotely update the unit firmware thanks to the data retrieved without the intervention of a local operator. Furthermore, the easy-to-use Rilheva interface allowed us to punctually analyse a large amount of data collected during the first months of operations and to verify historical trends of the main operating parameters.
Why would you recommend it?
Rilheva has a quick, “plug & play” setup process and fully customisable access levels, both from Italian HQ and the local assistance center. Avoiding local interventions for controlling and modifying parameters is an immediate economic advantage.
Last but not least, the plus of remotely learning about the real-world behaviour of our machines is an undeniable long-term benefit, which allows us to constantly improve the reliability of our products.